A while ago I was asked to create a bulk storage quiver for a Dark Age reenactment group. The very nice chap sent me a few photos of what he wanted and a specification. It had to hold 30 or 40 ‘blunts’, these are arrows with large rubber points used by reenactors. ‘Blunt’ arrows might not kill anyone, but they really hurt, like getting hit with an axe!
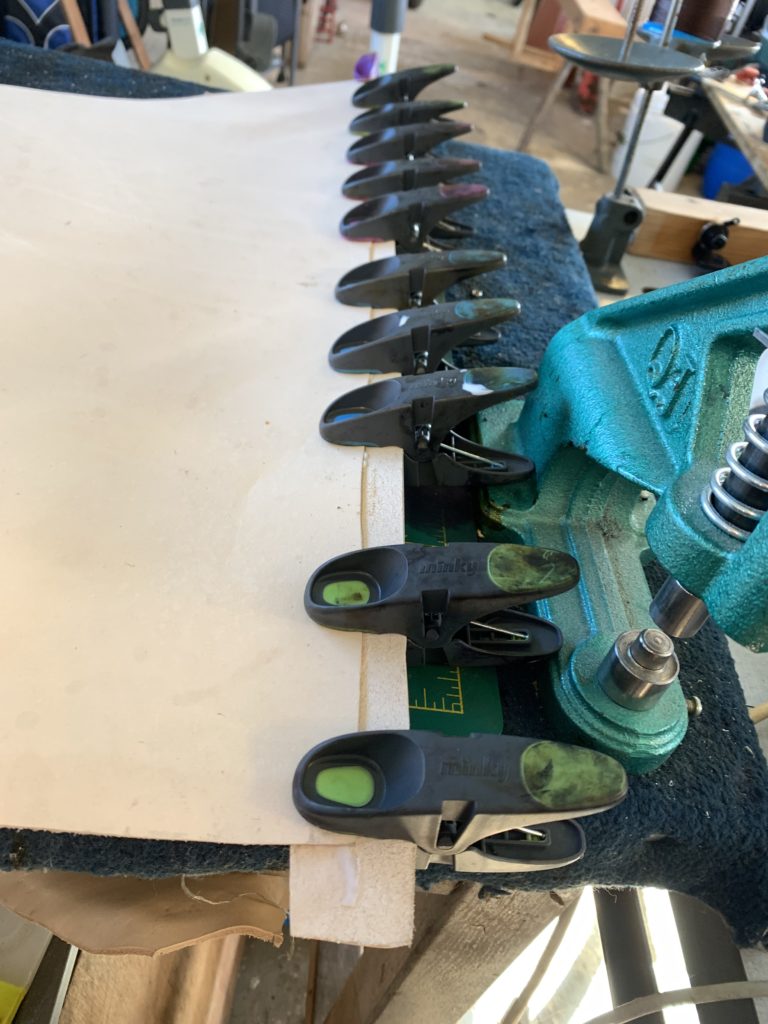
First things first, cut out sufficient 2mm veg tanned shoulder and add a reinforcing strip along the edge to be sewn.
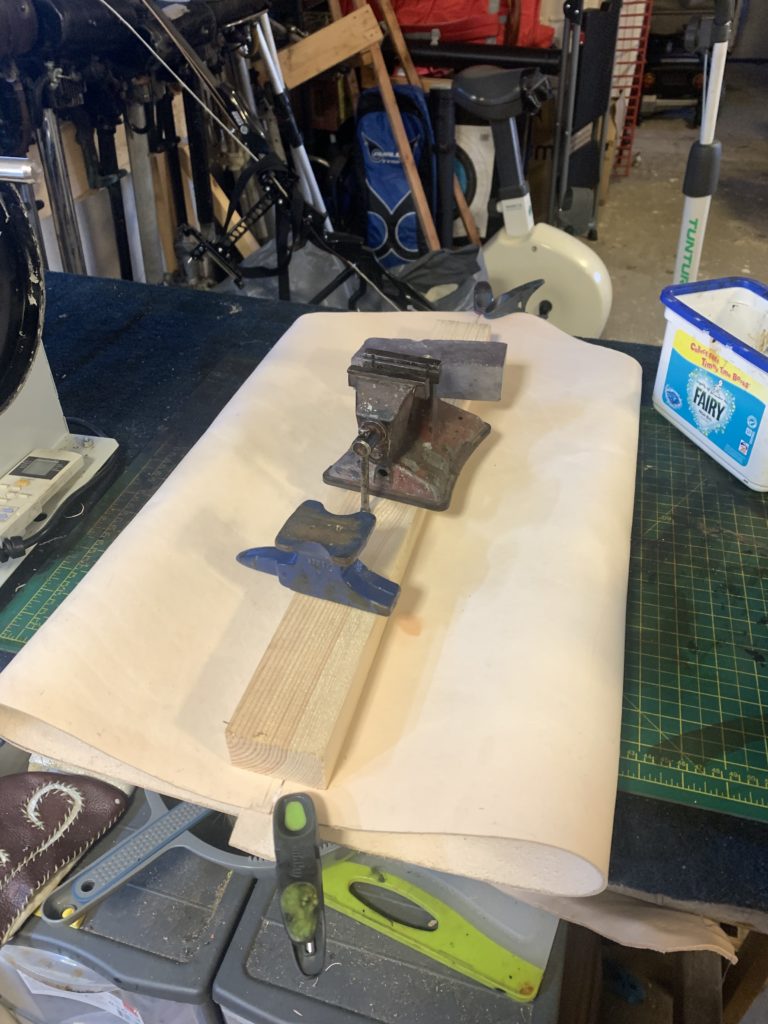
The facing edges can now be glued up prior to sewing…
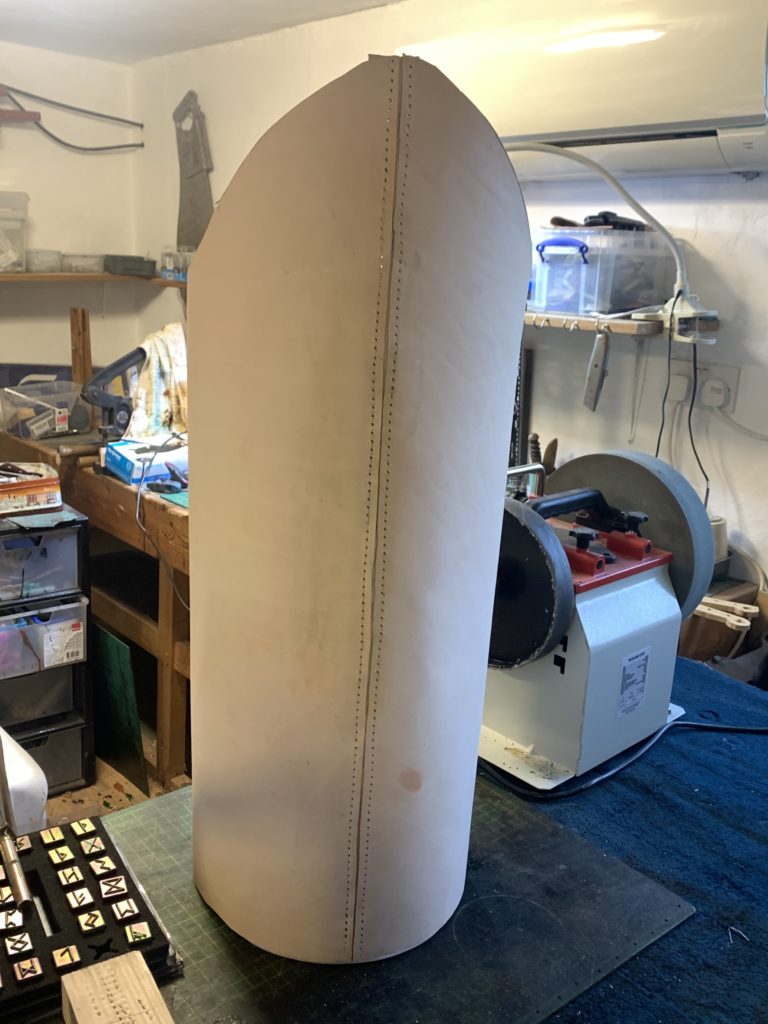
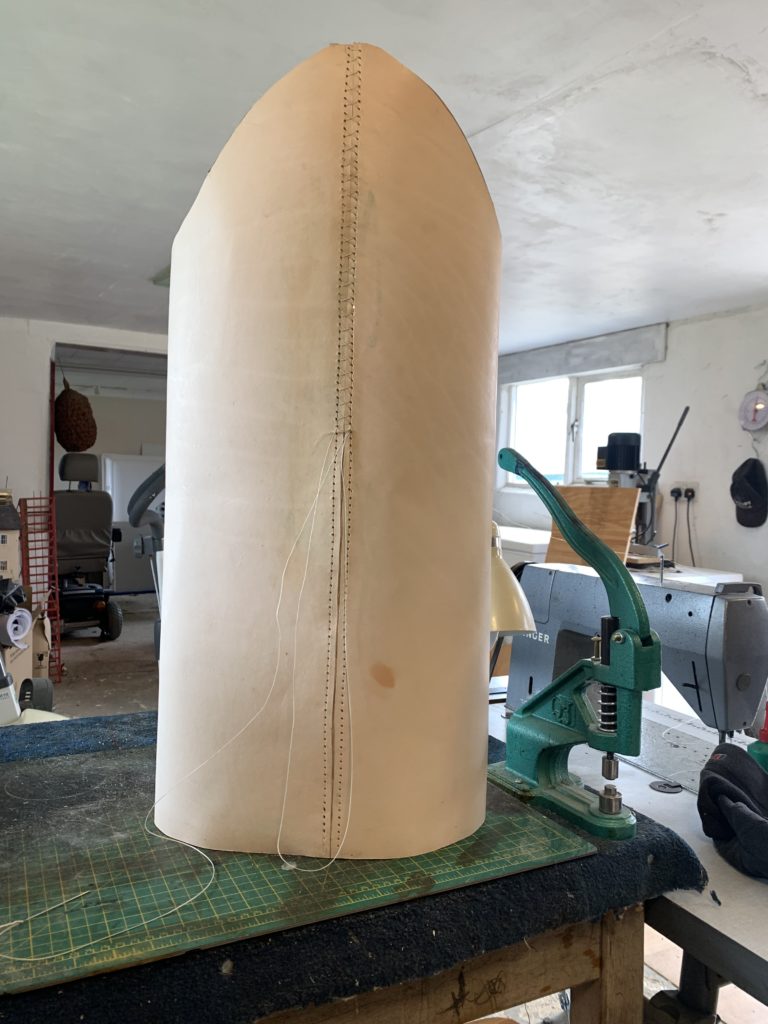
Using cross stitch the seam is sewn and pulled together, makes a change from the ubiquitous saddle stitch I use most of the time!…
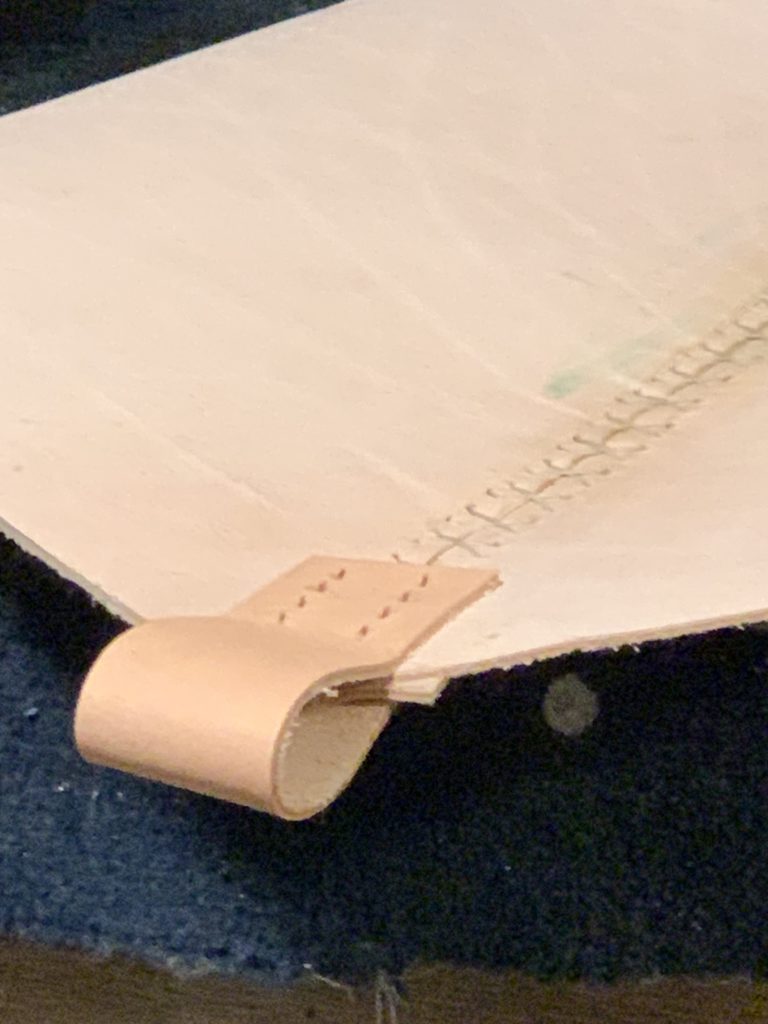
At this point the strap loops are added top and bottom,…
Next the tube is stained, the first of several coats…
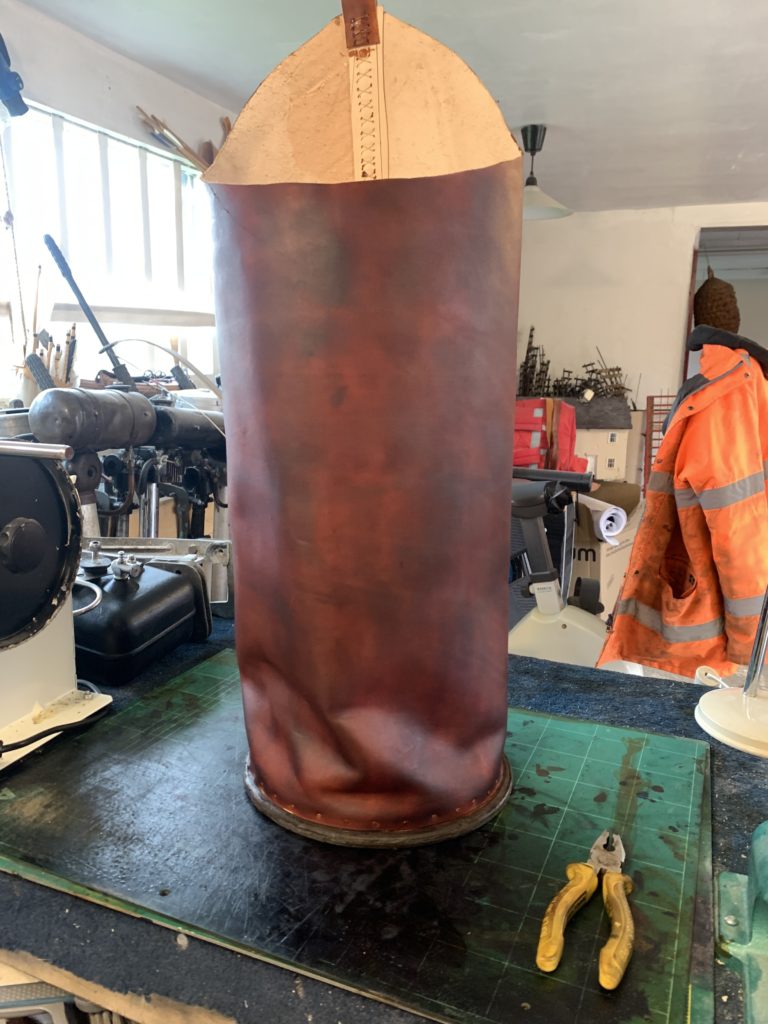
While waiting for the stain to dry, the base was cut out from two pieces of 12mm authentic Viking Age plywood…
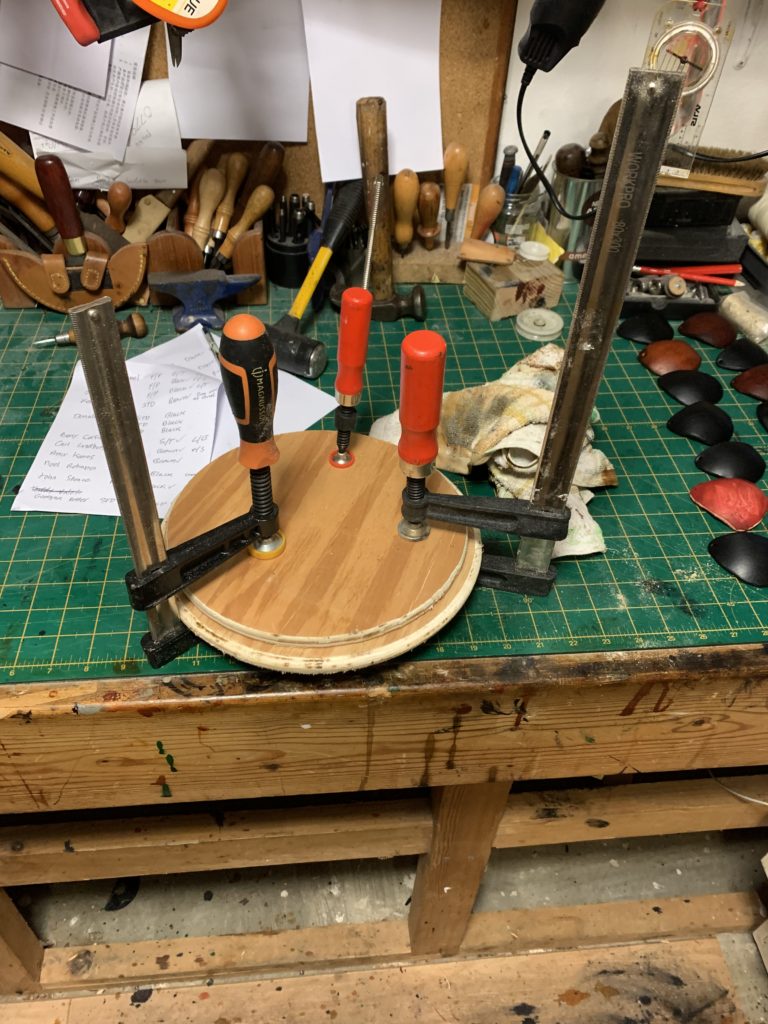
The tube and base are joined with copper tacks, roughly 2″ apart…
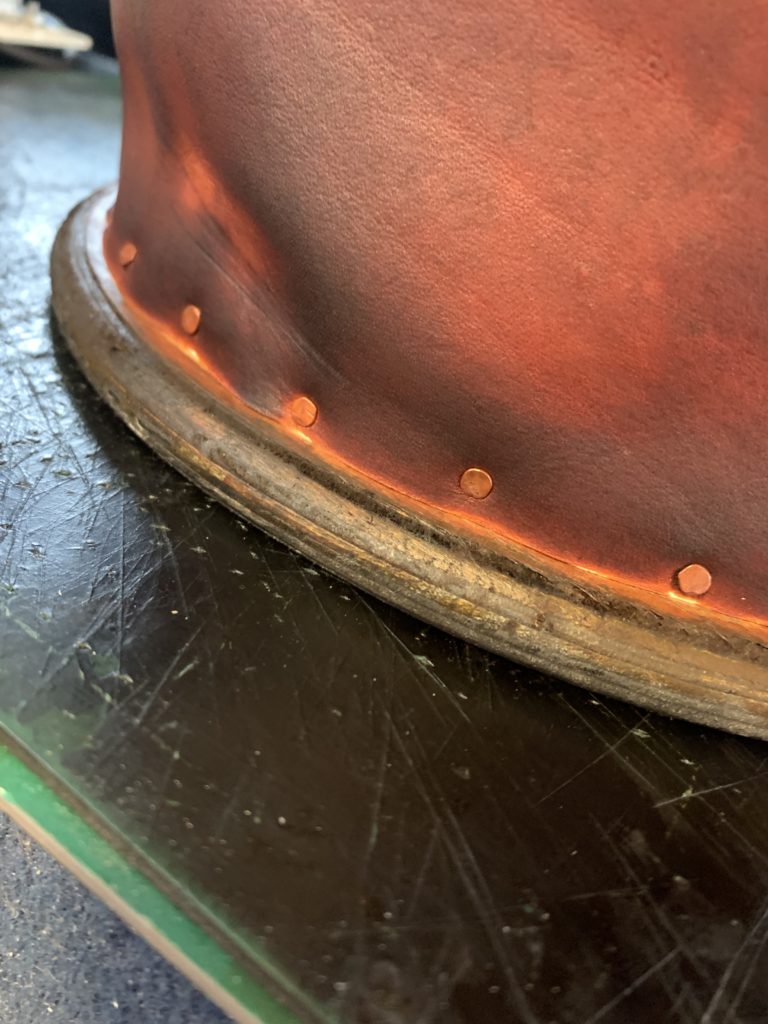
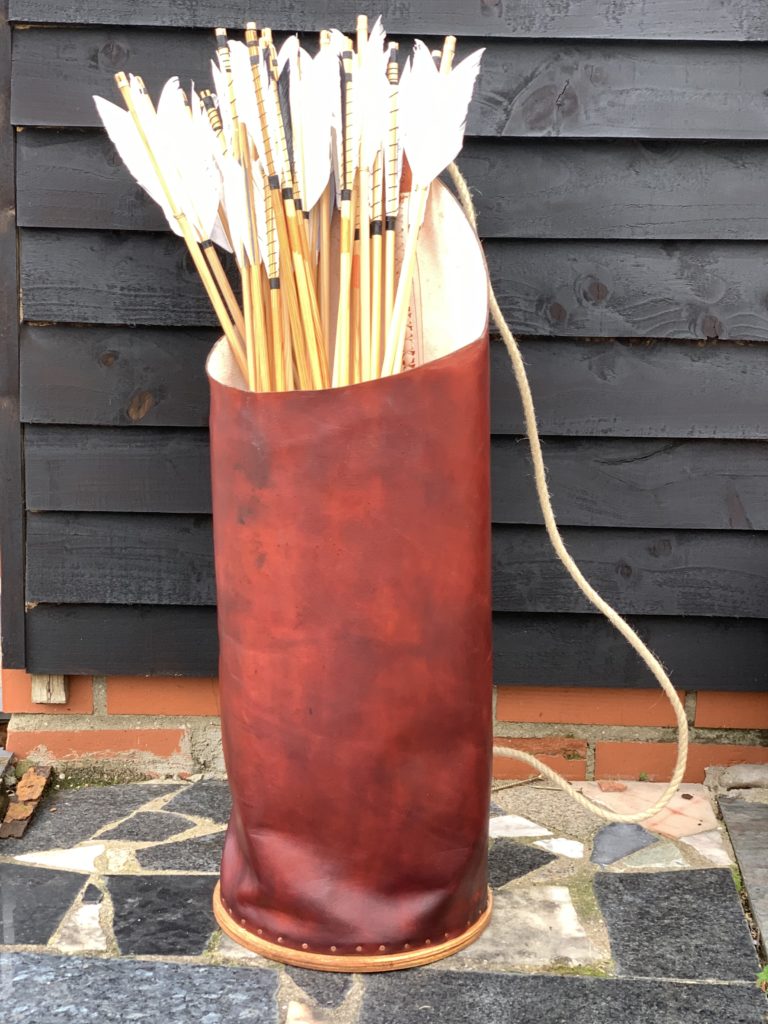
The finished Group Quiver. It easily accommodates 40 ‘blunts’ and is easy to carry from the Wick to the Arena, it is also handy having all the arrows in one place, safe from damage and less likely to be forgotten.
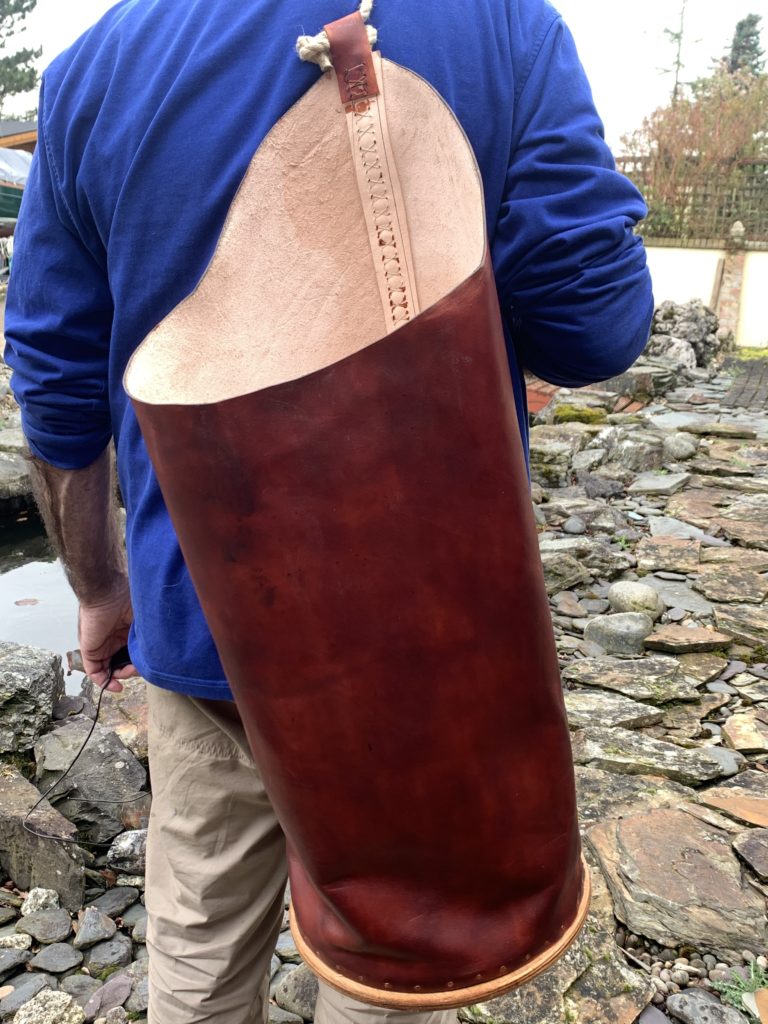
The customer that ordered this one was very happy with it. If you would like something similar check out my Etsy shop or drop me an email at blackwaterleather@gmail.com
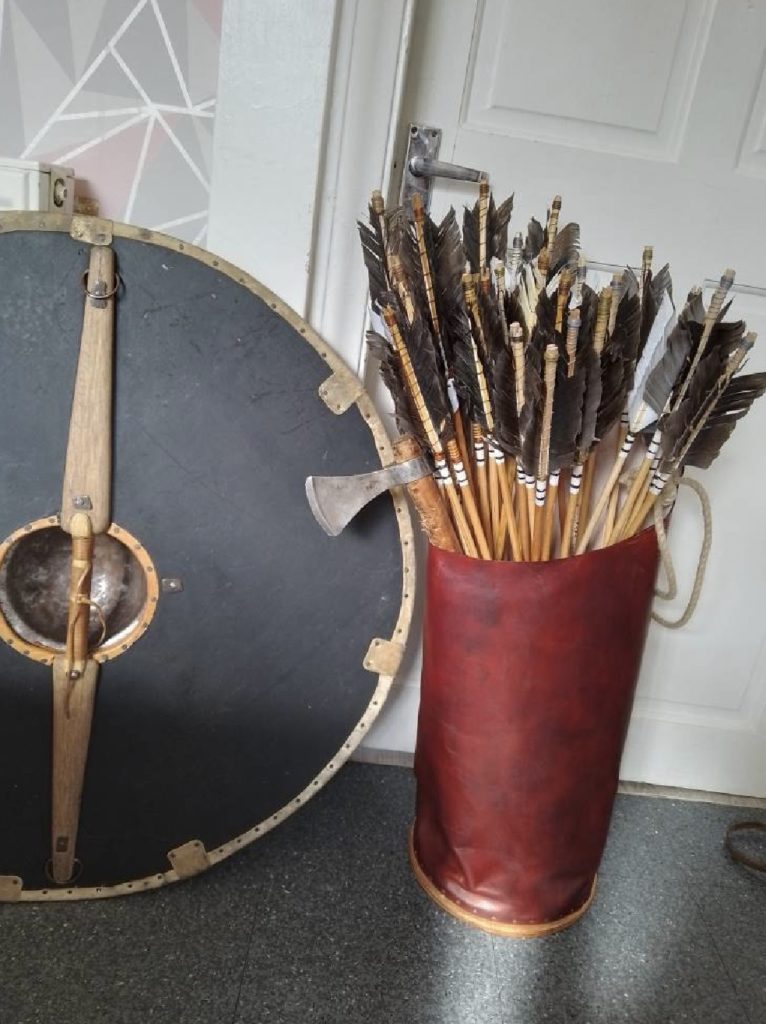